RUTHUNA® 479 Black Ruthenium Electrolyte
RUTHUNA® 479 Black is the perfect final finish for dark to black surfaces for decorative applications. The black ruthenium electrolyte is strongly acidic and has a long lifetime. It is easy to operate and primarily used for rack plating.
Depending on the degree of blackening, the abrasion resistance of the layers is good to very good. Applying a strike gold layer as an undercoat is strongly recommended. If palladium-nickel or palladium are used as undercoats, strike gold plating will partly not be necessary.
RUTHUNA® 479 Black is suitable for many decorative applications, for instance in the jewellery, bathroom fittings, spectacle frame and writing utensils industries.
The electrolyte can also be used for technical applications where up to 1 μm crack-free gray ruthenium layers are required.
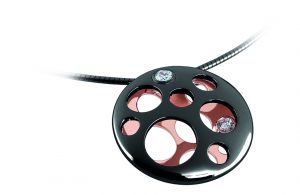
Electrolyte characteristics
Coating characteristics
Advantages
- For perfect decorative dark to black final finishes
- Degree of blackening adjustable
- Good colour constancy
- Strongly acidic electrolyte with long lifetime
- Simple bath maintenance
- Good to very good abrasion resistance
- Suitable for rack and barrel
RUTHUNA® 490 Black Ruthenium Electrolyte
RUTHUNA® 490 Black is a neutral electrolyte for brightness retaining, dark grey to anthracite coatings. The black ruthenium electrolyte is easy to operate and has a good colour constancy.
RUTHUNA® 490 Black permits the direct plating of copper, nickel, brass or bronze. This means that strike gold plating or strike plating with palladium or palladium alloys is not necessary, which leads to enormous precious metal cost savings.
The black ruthenium electrolyte is suitable for decorative applications, above all in the clothing industry. It can be used for rack and barrel plating operations. Due to its high abrasion resistance, subsequent lacquering is not necessary, reducing the number of further process steps. Its positive features make themselves apparent even at a low ruthenium concentration of just 2 g/l.
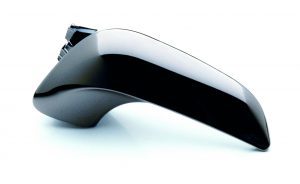
Electrolyte characteristics
Coating characteristics
Advantages
- Neutral black ruthenium electrolyte
- Simple bath maintenance
- Dark grey to anthracite coatings
- For decorative applications
- High abrasion resistance
- No lacquer finish is needed
- Good colour constancy
- Direct deposition on bronze or nickel possible
- No intermediate layers of expensive palladium or gold necessary
- Enormous precious metal cost savings
- Suitable for rack and barrel
RUTHUNA® 491 / 492 / 493 Ruthenium Alloy Electrolytes
The ruthenium electrolytes RUTHUNA® 491, 492 and 493 are neutral electrolytes from which decorative gray ruthenium coatings can be deposited. The electrolytes are easy to operate, and the deposits have a high color constancy and retain their brightness.
RUTHUNA® is used both as a final layer for decorative applications, e.g. on buttons, zippers and accessories in the apparel industry, and as a corrosion-resistant intermediate layer, e.g. to replace palladium. But functional properties, such as reduced sparking in current-conducting applications, also speak in favor of using RUTHUNA®. For example, the process is recommended for the following technical applications: Reed switches, injet printer foils, surfaces of catalytic converters, electrolytic electrodes.
In contrast to strongly acidic electrolytes, where pre-gold plating, or pre-coating with palladium or palladium-nickel is mandatory, materials such as copper, nickel, brass or bronze alloys can be used as undercoats under the ruthenium layer. Of course, palladium, palladium alloy and gold layers can also serve as base materials.
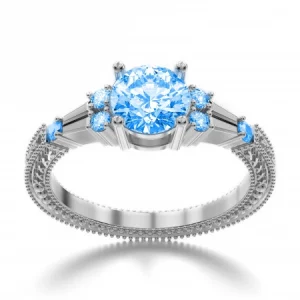
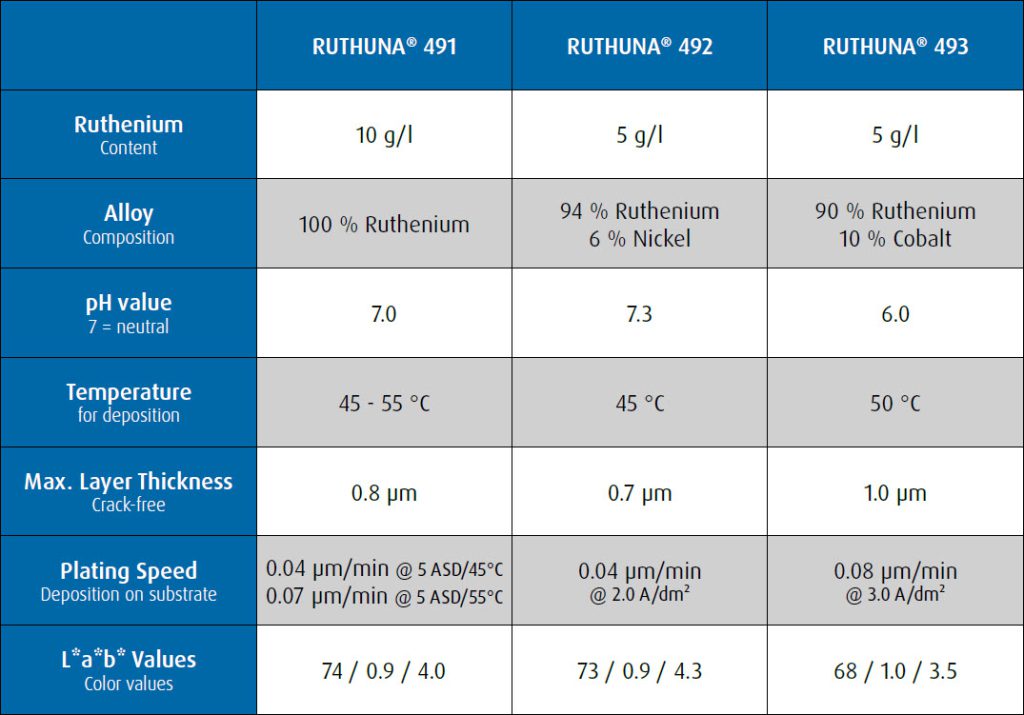
Advantages
- Easy electrolyte maintenance
- High color consistency
- Brightness-preserving
- As corrosion-resistant intermediate layers as a substitute for palladium
- Copper, nickel, brass or bronze alloys can be used as undercoats